Plastic Manufacturing Fundamentals Explaineds
Wiki Article
Lean Production for Beginners
Table of ContentsThe Main Principles Of Mfg The Best Guide To MfgThe 4-Minute Rule for Lean ManufacturingUnknown Facts About Hon Hai PrecisionOur Oem IdeasThe Greatest Guide To Additive Manufacturing
The message on this web page is an example from our complete White Paper 'Shot Moulding for Purchasers' - * Sample text * - for complete guide click the download switch above! Introduction This overview is meant for individuals that are looking to resource plastic mouldings. It gives a much needed understanding right into all that is involved with developing plastic parts, from the mould device needed to the moulding procedure itself.If you wish to check out additionally, the overview covers kinds of mould devices, along with special completing processes such as colours & plating. Words that are highlighted can be located in the glossary in the appendix ... Part I: Moulding: The Essentials The Benefits of Injection Moulding Plastic injection moulding is an extremely specific procedure that uses several advantages over other plastic processing techniques.
Accuracy is ideal for really elaborate parts. Contrasted to various other methods, moulding permits you to integrate even more attributes at really tiny tolerances. Have an appearance at the image to the. You can hold this moulding in the palm of your hand and also it has bosses, ribs, metal inserts, side cores and openings, made with a sliding shut down feature in the mould tool.
Indicators on Mfg You Need To Know
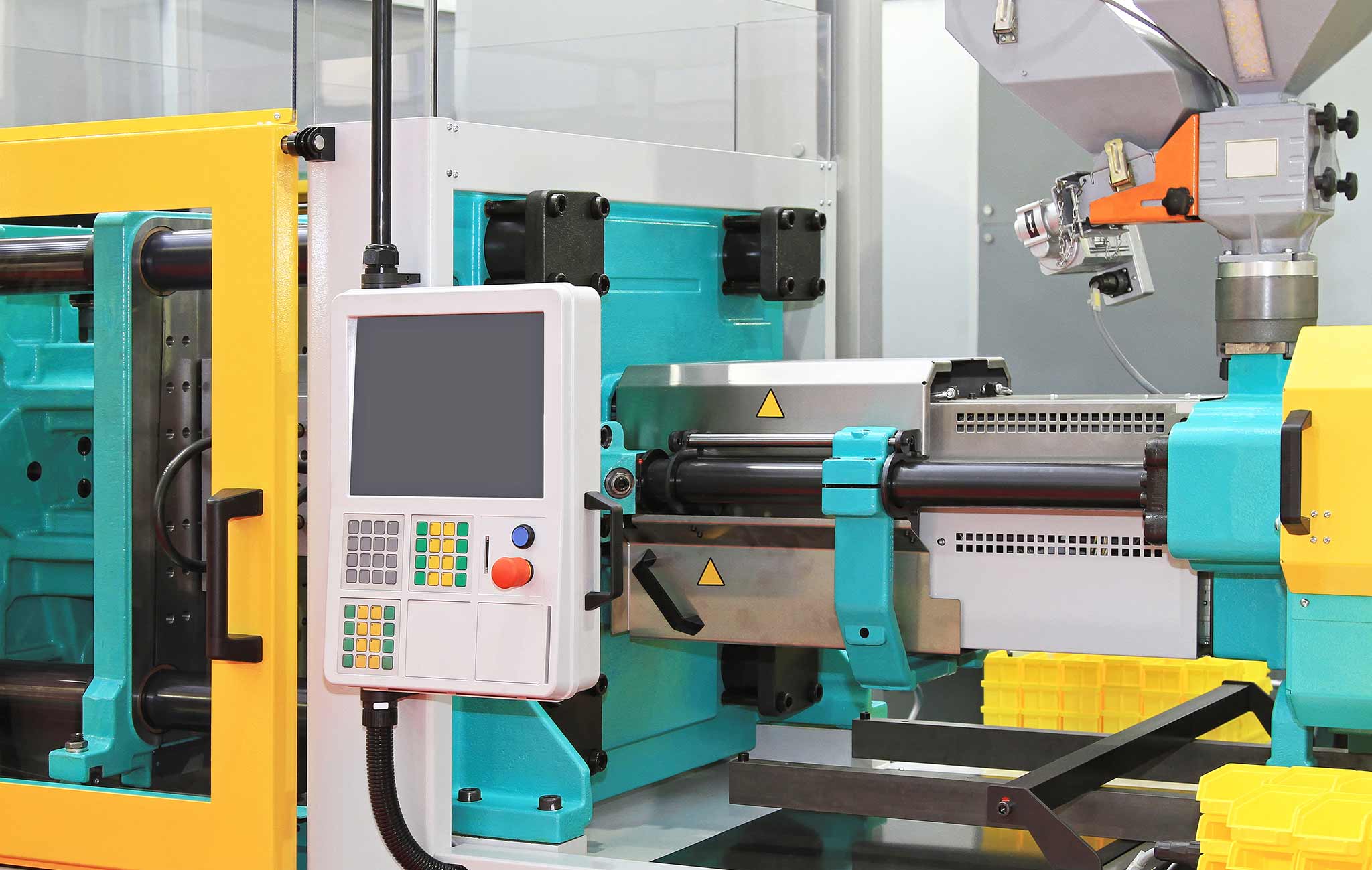

from material feed & melting; material injection; cooling time and ejection and also the re-closing of the mould tool ready device all set next cycle. Draft angles - The wall surfaces of a moulded part need to be a little tapered in the instructions in which the component is ejected from the mould tool, to permit the component to be ejected quickly.
Ejector stroke - The pressing out of ejector pins to expel the moulded part from the mould tool. Ejector stroke speed, size and timing needs to be meticulously managed to avoid damages to the ejectors and also mould tool, yet at the same time make the moulding cycle as brief as possible.

The Ultimate Guide To Oem
Ribs - When a plastic component has thin walls, ribs are included to the layout to make the thin walls stronger Side cores - Side activity which generates an attribute on a moulded component, at an opposing angle to the regular opening direction of the mould tool. oem. The their website side core requires to be able to withdraw as the plastic component can not be ejected or else.
Wall surfaces - The sides of a moulded component The text on this page is an example from our complete White Paper 'Injection Moulding for Purchasers'.
Manufacturing procedure for producing parts by infusing molten material into a mould, or mold Streamlined layout of the process Shot moulding (united state spelling: injection molding) is a manufacturing procedure for generating components by injecting molten material into a mould, or mold and mildew. Injection moulding can be done with a host of products generally consisting of steels (for which the process is called die-casting), glasses, elastomers, confections, as well as most typically thermoplastic and thermosetting polymers. Shot moulding is extensively utilized for making a selection of parts, from the tiniest components to whole body panels of vehicles. Shot moulding makes use of a special-purpose maker that has three parts: the injection device, the mould and also the clamp.
See This Report about Lean Production
, with the volume utilized of the previous being significantly higher.: 13 Thermoplastics are prevalent due to attributes that make them very appropriate for injection here are the findings moulding, such as ease of recycling, versatility for a wide variety of applications,: 89 and capability to soften and stream on heating.In several tooth cavity moulds, each cavity can be identical and develop the exact same components or can be unique and develop numerous different geometries during a single cycle. Moulds are normally made from device steels, yet stainless-steels and also aluminium moulds appropriate for sure applications. Aluminium moulds are usually improper for high quantity production or parts with narrow dimensional tolerances, as they have substandard mechanical properties as well as are more susceptible to put on, damages, and also contortion throughout the injection and also clamping cycles; nonetheless, aluminium moulds are cost-efficient in low-volume applications, as mould manufacture expenses and also time are significantly lowered.
When enough material has collected, the material is compelled at high stress and also velocity into the component creating tooth cavity. The precise quantity of shrinkage is a feature of the material being made use of, and can be reasonably predictable. To stop spikes in stress, the procedure normally uses a transfer position corresponding to a 9598% full dental caries where the screw shifts from a constant speed to a continuous pressure control.
The Single Strategy To Use For Hon Hai Precision
As soon as the screw reaches the transfer placement the packaging pressure is applied, which finishes mould dental filling as well as compensates for thermal shrinkage, which is quite high for thermoplastics loved one to several various other materials. The packing pressure is applied up until the entrance (tooth cavity entryway) strengthens. Because of its tiny dimension, eviction is typically the starting point to solidify via its entire thickness.: 16 Once eviction solidifies, no more material can enter the dental caries; appropriately, the screw reciprocates and acquires product for the following cycle while the material within the mould cools down to ensure that it can be expelled and also be dimensionally steady.Report this wiki page